Développée au sein de l’université de Rutgers, la technologie Solidia permet la réalisation d’un béton bas carbone pour la préfabrication. Une solution qui arrive en France avec le concours de LafargeHolcim.
Retrouvez cet article dans le n° 85 de Béton[s] le Magazine
![Solidia a développé sa propre chambre de cure pour injecter le dioxyde de carbone dans des blocs de béton, ou d’autres éléments. [©Solidia]](https://www.acpresse.fr/wp-content/uploads/2020/09/1-Solidia-MD.jpg)
Dans le secteur du ciment, la part des émissions de gaz à effet de serre est de l’ordre de 5 %1 à l’échelle mondiale et de 2,9 % sur le territoire français. Depuis l’ère pré-industrielle, le climat mondial s’est réchauffé d’environ 1 °C. A ce rythme, il pourrait atteindre + 1,5 °C entre 2030 et 2052 et + 3 °C d’ici 2100. L’industrie du bâtiment, donc celle du béton, s’empare de plus en plus de la question. Aux Etats-Unis, l’université de Rutgers, dans l’Etat du New Jersey, est à l’origine d’un nouveau béton bas carbone.
A partir de ces recherches, la start-up Solidia, qui est aussi le nom de la technologie, a été montée en 2010.
Cet article est réservé aux abonnés
des revues Béton[s] le Magazine et Process Industriels.
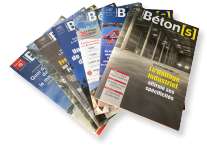
En plus de votre magazine, profitez d’un accès illimité à l’ensemble des contenus et services du site www.acpresse.fr :
- Lecture de l’intégralité des dossiers thématiques, reportages chantiers, fondamentaux, histoire de la construction…
- Consultation des indicateurs économiques (chiffres et analyses)
- + vos newsletters pour suivre l’info en continu