Le cimentier suisse Holcim vient d’annoncer avoir produit le premier clinker au monde composé à 100 % de minéraux issus du recyclage. Quelque 2 000 t fabriquées en 2 j sur le site d’Altkirch, en Alsace.
![Holcim annonce la production du premier clinker composé à 100 % de minéraux issus du recyclage. [©ACPresse]](https://www.acpresse.fr/wp-content/uploads/2022/06/Holcim-Recyclage.jpg)
Le cimentier suisse Holcim vient d’annoncer avoir produit le premier clinker au monde composé à 100 % de minéraux issus du recyclage. L’opération s’est déroulée sur le site de la cimenterie d’Altkirch, dans le département du Haut-Rhin. « Quelque 2 000 t de clinker ont été fabriquées à partir de matériaux recyclés, indique le groupe Holcim. De quoi permettre de préserver les ressources naturelles de la carrière, en économisant l’équivalent de 3 000 t de matières premières extraites. Ce clinker n’a pas été intégré à la production du site. Mais il est en cours de transformation en ciment 100 % recyclé sur un autre site du groupe en France, avec des ajouts provenant aussi de matériaux recyclés… »
Dix matériaux recyclés dans la composition
L’essai s’est étalé sur 2 j sans arrêt, avec un monitoring permanent suivi par une équipe spéciale composée de 10 personnes. Parmi elles, des experts du centre de recherche de L’Isle-d’Abeau, les collaborateurs du site, la direction qualité de Lafarge et la direction industrielle. En effet, il existait plusieurs inconnues liées à cette grande première : quelle sera la réaction du mélange ? Quel sera son comportement à la cuisson ? Quel sera l’impact éventuel sur le four ?
L’objectif prioritaire de ce test de production était avant tout de valider la technologie. « Nous avons estimé à – 10 % la baisse des émissions de CO2 liée à la décarbonatation des matériaux recyclés utilisés, comparé à un clinker non recyclé, reprend le groupe Holcim. Une performance intéressante même si ce n’était pas la première recherchée. Ce que nous avons surtout réussi, avec cette première mondiale, c’est de démontrer qu’il est aujourd’hui possible de produire un clinker correspondant à la norme à partir de matériaux 100 % recyclés. » Au-delà de l’exploit du 100 % recyclé, ce test a permis de fare avancer à grand pas le sujet de l’ingénierie nécessaire pour intégrer encore plus de déchets dans le cru. Il fait donc progresser l’ensemble des usines du groupe Holcim.
Dans le détail, l’industriel a utilisé des matières premières alternatives toutes issues de l’économie circulaire et provenant, en grande partie, de sources locales. A savoir de la région Grand Est. « Dix produits recyclés différents ont été rassemblés, afin de disposer de tous les éléments nécessaires pour atteindre la composition chimique cible du clinker, reprend Holcim. Ceci, dans le but d’une conformité avec la norme ciment. Ainsi, chaque matériau a été caractérisé d’un point de vue chimique en laboratoire. » Le cimentier refuse de les citer tous, « pour des raisons évidentes de confidentialité. » Mais indique tout de même la présence de cendres de bois ou de déchets du traitement des minéraux…
Une cuisson dans un four à 1 450 °C
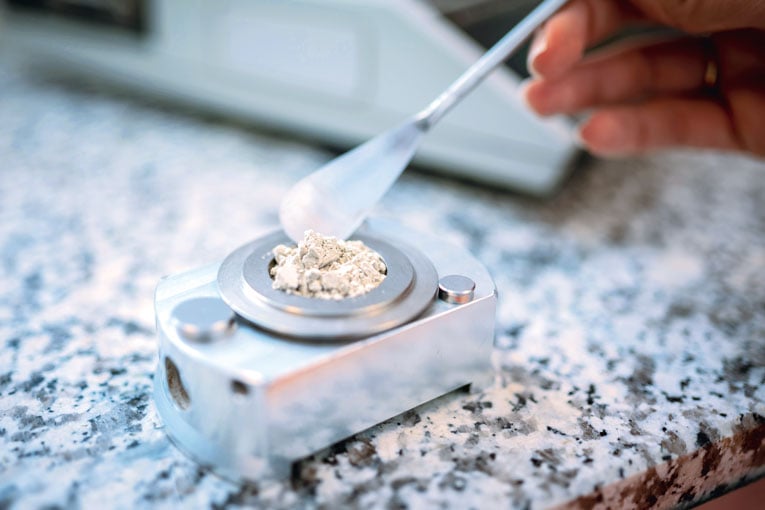
Côté fabrication, le processus est similaire à celui du clinker normal, une fois les constituants rassemblés sur le site. Pour commencer, les matériaux recyclés sont pré-mélangés dans la carrière où ils sont stockés, de façon à constituer une farine crue homogène. L’étape 2 est celle de la cuisson dans le four rotatif de la cimenterie, à la même température que les matériaux naturels habituels (calcaire et argile pour l’essentiel). C’est-à-dire à 1 450 °C. Viennent ensuite les classiques opérations de broyage et d’ajouts d’additions complémentaires qui permettront d’obtenir un ciment. Nous ne sommes donc pas ici en présence d’un véritable clinker bas carbone direct. Mais il permet une décarbonation indirecte du secteur cimentier à travers l’économie de matières premières vierges.
Pour Holcim, cette première est un succès et le clinker obtenu est conforme aux objectifs de qualité fixés, ainsi qu’à la norme ciment. Il sera utilisé pour produire du ciment 100 % recyclé. En le mélangeant avec de l’eau recyclée, des armatures produites avec des aciers recyclés et d’autres composants valorisés, il deviendra possible de réaliser un béton 100 % recyclé. Holcim annonce la mise en œuvre d’un tel produit dès 3e trimestre 2022 !
Inscrit dans la trajectoire “net-zéro”
« Cette percée montre ce qu’il est possible d’accomplir lorsque vous combinez l’expertise d’Holcim en matière de recyclage avec sa position producteur de ciment, indique Edelio Bermejo, directeur du Holcim Innovation Center. Développer un clinker 100 % recyclé nous fait franchir une étape supplémentaire dans notre quête de la construction circulaire. »
Le nouveau clinker s’inscrit dans la trajectoire “net-zéro” d’Holcim pour décarboner l’environnement bâti. Ainsi, en 2021, le cimentier a recyclé 54 Mt de matériaux dans l’ensemble de ses activités dans le monde. Et prévoit de doubler ce taux d’ici 2030. Pour construire du neuf à partir de l’ancien, il intensifie le recyclage des déchets de construction et de démolition en nouveaux matériaux de construction. L’objectif de la démarche est d’atteindre 10 Mt d’ici 2025. En 2021, Holcim en avait recyclé 6,6 Mt. Et, en Suisse, il a lancé le premier ciment vert au monde contenant 20 % de déchets de construction et de démolition recyclés. Ceci, dans sa gamme EcoPlanet.