Véritable roche liquide à température ambiante, le béton offre un usage d’une incomparable commodité, ce qui le rend difficile à remplacer. En France, plus de 80 % du patrimoine bâti est en béton.
Faisant suite à l’article “Un béton vert est-il possible #1 ?”, ce présent opus est la seconde partie proposée par l’Ifstaar, qui travaille sur le recyclage du béton de démolition.
III – Le comportement à l’état frais*
Notre société repose principalement sur l’utilisation du béton dans nos constructions. Il devient primordial de limiter ses impacts sur l’environnement. L’enjeu se situe donc au niveau de la fabrication du ciment, qui est une source non négligeable d’émissions de CO2. Le ciment est un liant qui, comme une colle, a pour fonction de solidariser entre eux les ingrédients du béton. Les chercheurs de l’Ifsttar veillent à ce que l’introduction de ciments à faibles impacts environnementaux ne détériore pas les propriétés fondamentales du béton…
a – Des ciments à faibles impacts environnementaux
La production d’un ciment à faibles impacts environnementaux constitue un défi majeur pour notre société actuelle. Ce défi peut être résolu, en partie, si la quantité de clinker (composé principal du ciment) est diminuée dans le mélange. L’une des pistes les plus prometteuses est de le remplacer par des sous-produits provenant d’autres industries :
- laitier de hauts fourneaux,
- fumée de silice,
- déchets de verre,
- déchets agricoles…
Ou par des ressources minérales naturelles (calcaire, argile, bauxite…). Cet axe de recherche a fait l’objet de nombreuses publications scientifiques(1, 2)et d’une évolution progressive des normes.
Pourtant, des questions relatives à l’effet de ces matériaux sur l’écoulement du béton subsistent (principe de rhéologie). Elles se posent en ce qui concerne la diversité des produits et les proportions à utiliser3. Le comportement à l’état frais de ces nouveaux ciments a un impact important sur les étapes de mise en œuvre du béton (malaxage, pompage, coffrage…). Les conséquences peuvent être considérables sur les propriétés d’usage du béton à l’état durci (résistance mécanique et durabilité).
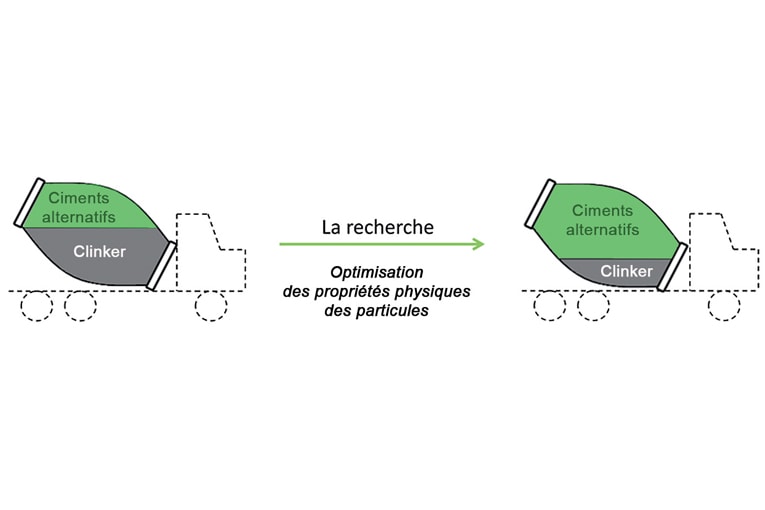
b – Un comportement sous haute surveillance
L’écoulement d’une pâte de ciment (comportement rhéologique4) est dicté par plusieurs phénomènes :
• les propriétés physiques des particules (distribution de tailles, formes, surfaces spécifiques, compacité…),
• les interactions physico-chimiques entre particules,
• l’encombrement du système (taux d’occupation du volume par des particules solides).
Il est donc nécessaire de tenir compte de ces paramètres. Ils peuvent être modifiés lorsque le clinker est remplacé, même en partie, par un autre produit.
Les travaux de recherche permettent ainsi d’identifier et de classifier les phénomènes physico-chimiques modifiés par l’intégration d’ajouts minéraux. Ces résultats contribuent au développement de nouvelles pistes pour contrôler le comportement, à l’état frais, de ces ciments alternatifs.
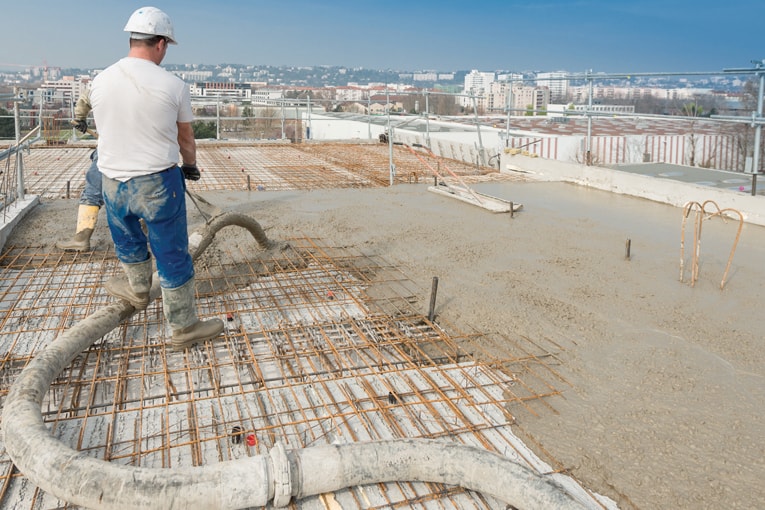
c – Des matériaux de plus en plus performants
Les propriétés physiques, définies par l’étude (forme, distribution de taille, compacité et surface spécifique), permettent aux producteurs de sous-produits industriels ou de ressources minérales naturelles d’augmenter les performances de leurs matériaux. En améliorant les procédés de broyage, de filtration ou de séparation des particules, il est possible de favoriser l’incorporation de leurs matériaux dans le ciment.
Ces travaux permettent donc d’optimiser le choix des nouveaux liants et la quantité à introduire pour obtenir un béton plus écologique. De nouvelles perspectives en faveur d’un béton vert.
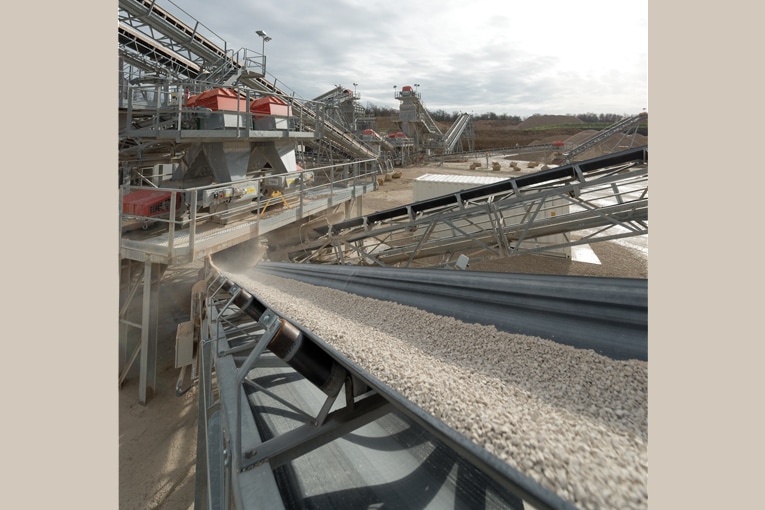
IV – La piste des granulats**
Les granulats constituent la partie la plus importante d’un béton : environ les deux tiers de la masse. Or, la demande en granulats est très forte dans les agglomérations. Paris et la petite couronne consomment 13 Mt/an (livre blanc UNPG). Et ce besoin va augmenter dans les années qui viennent. En effet, avec les projets du Grand Paris, on estime que la demande augmentera de 5 Mt/an (Driee d’Ile-de-France). Alors que la région Ile-de-France a un problème de ressources et est déjà importatrice de près de la moitié des granulats qu’elle consomme… Les bétons représentent 42 % de la consommation totale. Ainsi, économiser les granulats pour faire du béton est un enjeu majeur.
a – Le recyclage des bétons dans les bétons
Alors que la demande en granulats est de plus en plus forte, le volume de déchets générés par la déconstruction augmente. Et va devenir très important dans le futur. Les matériaux cimentaires représentent environ le tiers de ces déchets, mais ils sont très peu utilisés pour refaire des bétons. Or, le coût environnemental de ces déchets augmente. Et justifie les recherches entreprises pour démontrer que leur valorisation réduit leur impact environnemental.
C’est pourquoi, dès 2008, l’Ifsttar a lancé une recherche en partenariat avec la profession en vue d’optimiser la formulation des bétons avec des granulats recyclés5. Cette action s’est prolongée à partir de 2012, dans le cadre du projet national Recybéton6. Ce projet avait pour objectif d’accroître la réutilisation des matériaux issus des bétons déconstruits comme constituants des nouveaux bétons. Il regroupait des industriels et des centres de recherche, dont l’Ifsttar.
Valoriser le recyclage des bétons
Adossé à Recybéton, Ecoreb (Ecoconstruction par le recyclage du béton) est un projet ANR complémentaire. Il permet le développement de nouveaux outils, en se fondant sur l’existant pour les bétons traditionnels. Il s’agira de quantifier la demande en eau des granulats recyclés et de caractériser la qualité des interfaces pâtes/granulats. Le projet vise aussi à fournir un outil de prédiction des résistances des bétons recyclés et de leur comportement sous sollicitations endogènes (retrait, chaleur d’hydratation…) et sous sollicitations externes (charges mécaniques, neige…).
De son côté, le projet ANR Crac (Carbonated Recycled Aggregates for Concrete) s’est intéressé au piégeage de CO2 par les granulats de bétons recyclés. Ainsi que le projet national FastCarb – actuellement en cours -, qui étudie la recarbonatation accélérée des granulats recyclés de béton. Ce traitement permet d’améliorer les caractéristiques physiques et mécaniques de ces granulats et d’optimiser le bilan CO2des bétons.
L’ensemble de ces recherches doit valoriser le recyclage des bétons et, ainsi, préserver la ressource naturelle en granulats.
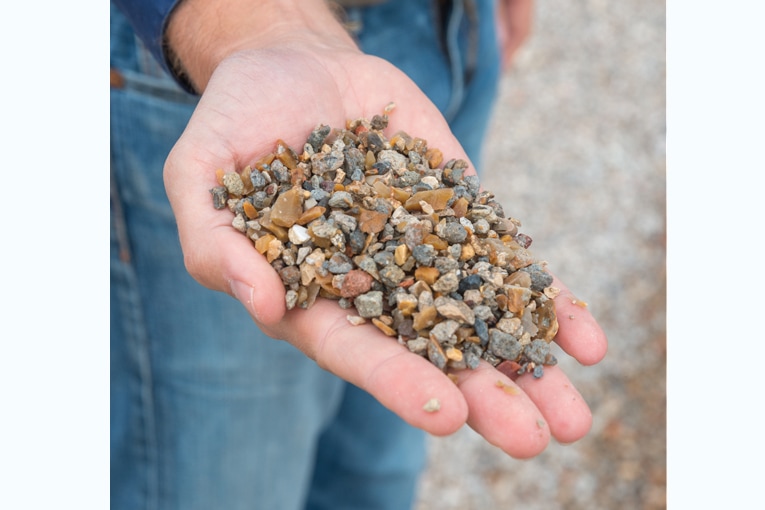
b – Le cas du Lyon Tunnel Ferroviaire
La future liaison ferroviaire entre Lyon et Turin, dont le promoteur est Lyon Tunnel Ferroviaire (LTF), comportera deux tunnels, d’une longueur cumulée 65 km. Leur creusement générera 18,8 Mm3 de déblais. Dans le cadre d’une démarche de développement durable, près d’un quart de ces déblais doit être valorisé en granulats pour le revêtement en béton des tunnels. Outre son intérêt économique, cette solution doit permettre d’éviter l’excavation dans de nouvelles carrières, et de limiter ainsi les transports de déblais et de granulats par route.
Toutefois, ces matériaux d’excavation contiennent une quantité de sulfates 10 à 20 fois supérieure à celle préconisée par les normes actuelles. Ceci peut générer une détérioration du béton par formation de produits expansifs, tels que l’ettringite ou la thaumasite7. Dans cette optique, le département “Matériaux et Structures” de l’Ifsttar participe à une recherche partenariale avec :
- LTF,
- LafargeHolcim,
- Vicat et
- Setec-Lerm.
L’objectif est d’acquérir des connaissances sur le comportement des sulfates présents dans ces granulats. Et d’élaborer de nouvelles formulations de béton adaptées, afin d’éviter tout problème de détérioration en fonction des conditions environnementales.
La valorisation des déblais du tunnel ne doit toutefois pas être réalisée au détriment des autres propriétés de mise en œuvre et de durabilité nécessaires à un tel ouvrage. Ainsi, cette recherche sera complétée par une démarche performantielle globale et prédictive de la durabilité des formules de béton. Ces dernières seront retenues sur la base des indicateurs de durabilité préconisés dans le guide de l’AFGC intitulé “Conception des bétons pour une durée de vie donnée des ouvrages”.
c – Les matériaux biosourcés
Afin de réduire l’impact environnemental, lié à l’utilisation des matériaux de construction, et d’améliorer l’efficacité énergétique des bâtiments, des matériaux d’origine végétale doivent être privilégiés. Issus pour l’essentiel de l’industrie agricole, des granulats végétaux sont enrobés par des microstructures du béton de chanvre (dont les liants minéraux sont à base de chaux) pour former des matériaux isolants, appelés “bétons végétaux”. Leur utilisation permet donc d’améliorer le bilan écologique global du bâtiment. Et d’apporter de multiples propriétés, comme :
- les performances thermiques et acoustiques et
- de la légèreté à la construction.
Pendant toute leur durée de vie, ces bétons contribuent aussi au stockage du CO2.
Cependant, de nombreux blocages subsistent et limitent le développement de ce type d’éco-matériaux. Plus de connaissances sur le vieillissement de ces produits sont nécessaires, les premières constructions datant des années 1985/1990. C’est pourquoi l’Ifsttar mène des travaux de recherche sur la durabilité de ces matériaux. Ces travaux concernent l’évolution de leurs propriétés, en fonction de leurs conditions d’utilisation.
Pendant deux ans, des éprouvettes de bétons de chanvre ont été soumises, en laboratoire, à plusieurs vieillissements accélérés. Leurs propriétés (mécaniques, thermiques et acoustiques, régulateur d’humidité) ont été caractérisées pendant cette période et reliées à leur composition chimique et à leur microstructure. Ces nouvelles connaissances ont permis de montrer la stabilité des performances de ces bétons végétaux, lorsqu’ils sont soumis à des environnements représentatifs de leurs conditions réelles d’utilisation.
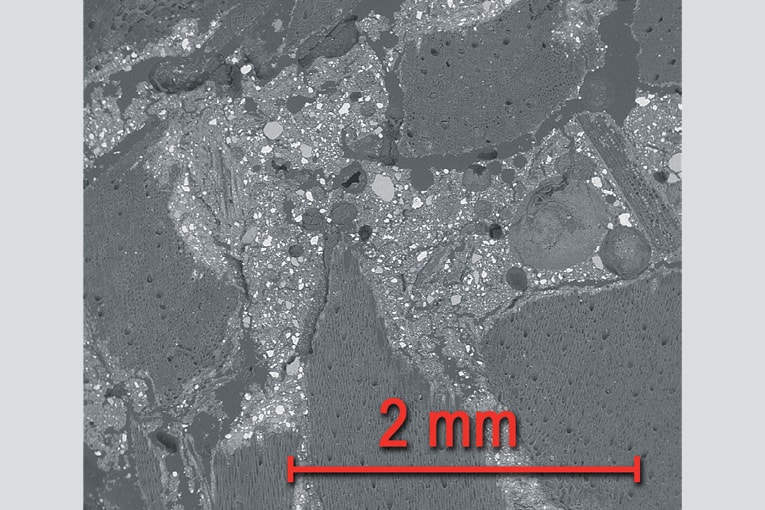
V – Le piégeage du CO2***
Sur 1 kg de ciment produit en cimenterie, l’émission de CO2 est de 600 à 700 g en moyenne. Compte tenu des quantités impressionnantes de ciment produites à l’échelle mondiale, l’industrie cimentière serait donc à l’origine de 5 à 7 % des émissions mondiales anthropiques de CO2. Près de la moitié de cette émission est due à la nature chimique même du clinker (principal composant du ciment), dont la fabrication est obtenue par décarbonatation du calcaire8.
a – Le principe de carbonatation des bétons
Le mélange d’eau et de ciment conduit à la formation d’hydrates à l’origine de la résistance des bétons. La présence de CO2dans l’atmosphère, même en faible quantité (0,038 %), provoque une carbonatation9irréversible et lente de ces hydrates. A l’échelle des temps géologiques, la carbonatation est ainsi à même de piéger (réabsorber) la part du CO2chimiquement émis par la cimenterie lors de la calcination du calcaire. Les conséquences de la carbonatation du béton sont cependant diverses, en fonction du moment où elle intervient, c‘est-à-dire durant la phase de service de l’ouvrage ou après sa démolition.
L’Ifsttar travaille depuis de nombreuses années sur la carbonatation des bétons au cours de la phase de service des structures en béton armé. En effet, le CO2de l’atmosphère se diffuse dans la porosité du béton et se dissout, en formant des acides au contact de la solution interstitielle. Ce phénomène a pour principale conséquence d’abaisser le pH du milieu (du béton) et de conduire à la corrosion des armatures. L’Ifsttar propose des modèles de prédiction de la durée de vie vis-à-vis du risque de corrosion. Ils peuvent être utilisés pour orienter la formulation du béton, le dimensionnement des structures…
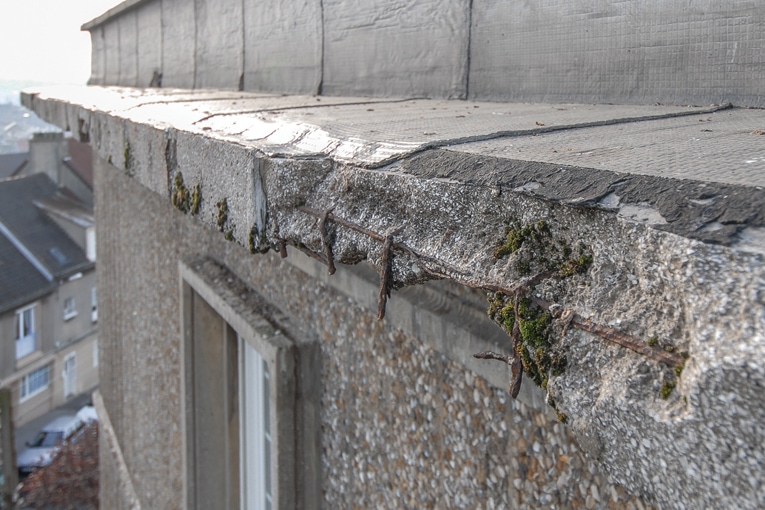
b – Une aubaine pour améliorer le “bilan carbone” du béton
A l’inverse des conséquences néfastes de la carbonatation sur la pérennité des structures en béton armé, ce phénomène peut s’avérer bénéfique du seul point de vue du béton. En effet, dans le cadre d’éléments non armés, la carbonatation peut contribuer à piéger du CO2et à améliorer le “bilan carbone” du béton10. Le béton possède une capacité naturelle à capter CO2. Mais lorsqu’il est sous la forme d’un élément de structure de bâtiment, cette réaction s’effectue sur une petite surface et est, par conséquent, très lente. En revanche lorsqu’il est concassé pendant la phase de démolition, la surface en interaction avec l’atmosphère augmente et la réaction du piégeage du CO2est accélérée.
Depuis 2018, le projet national FastCarb étudie comment encore accélérer ce phénomène, afin de reprendre environ 20 % du CO2libéré initialement lors de la fabrication du ciment, ayant servi à la formulation du béton. Soit entre 40 et 60 kg de CO2par m3de béton. En collaboration avec de nombreux partenaires, l’Ifsttar étudie comment le procédé peut être optimisé. Le projet permettra aussi une démonstration à un niveau industriel et des applications sur des chantiers utilisant des granulats recyclés.
c – L’utilisation des granulats de béton de démolition
La carbonatation présente un autre avantage : elle améliore les propriétés de microstructure et mécaniques du béton. Ainsi, lorsque le piégeage du CO2est optimisé, les granulats recyclés obtenus sont de meilleure qualité et l’on peut les réutiliser pour fabriquer un nouveau béton. Un avantage indéniable lorsque l’on sait qu’il existe en France une quantité importante de bâtiments en fin de vie voués à la destruction. L’Ifsttar travaille donc sur la mise à profit de la carbonatation pour améliorer les propriétés des granulats de béton de démolition en vue de les recycler pour fabriquer du nouveau béton.
Janvier 2020
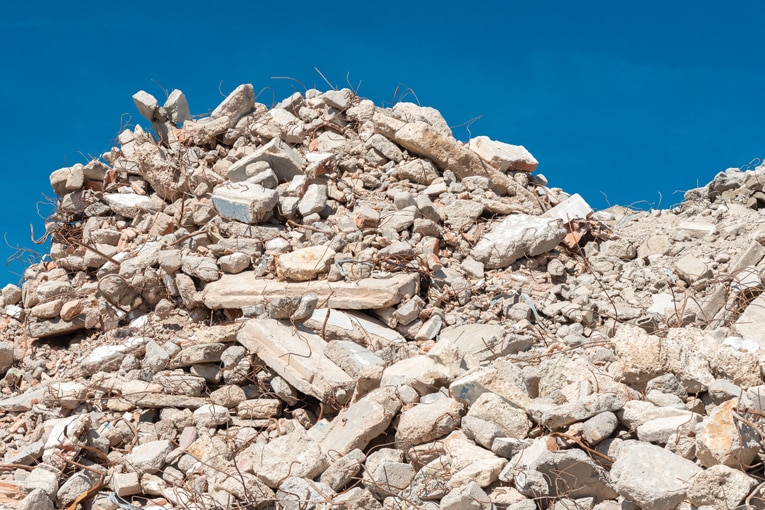
Découvrez la partie #1 de l’article “Un béton “vert” est-il possible ?”
*Hela Bessaies-Bey
Chercheuse en physico-chimie des matériaux au département Mast (Matériaux et structures), Laboratoire CPDM (Comportement physico-chimique et durabilité des matériaux), à l’Ifsttar.
**Jean-Michel Torrenti
Directeur du département Mast (Matériaux et structures), à l’Ifsttar
***Mickaël Thiéry
Chercheur (aujourd’hui, adjoint au sous-directeur de la qualité et du développement durable dans la construction, à la Direction générale de l’aménagement, de la nature et du logement)
1M. C. G. Juenger, R. Siddique, Recent advances in understanding the role of supplementary cementitious materials in concrete, Cement and Concrete Research 78 (2015) 71–80.
2B. Lothenbach, K. Scrivener, R. D. Hooton, Supplementary cementitious materials, Cement and Concrete Research 41 (2011) 1244–1256.
3R. J. Flatt, N. Roussel, C.R. Cheeseman, Concrete : An eco material that needs to be improved, Journal of the European Ceramic Society, 32 (2012) 2787-2798
4N. Roussel, A. Lemaitre, R. J. Flatt, P. Coussot, Steady state flow of cement suspensions : A micromechanical state of the art, Cem. Concr. Res. 40 (2010) 77–84.
5Thèse de Duc-Tung Dao. Plus d’informations dans le n° 122 de la revue “Routes”.
6www.pnrecybeton.fr
7L’ettringite et la thaumasite sont deux composés minéraux, résultant de l’attaque de certaines phases du ciment hydraté par les sulfates.
L’ettringite peut générer une expansion et la fissuration du béton.
La thaumasite conduit à une perte des propriétés mécaniques du béton par consommation des silicates de calcium hydratés.
Les conditions de formation de ces composés dépendent à la fois de la formulation du béton et des conditions environnementales.
8Le calcaire (CaCO3) constitue avec l’argile la matière première du clinker. La fabrication du clinker passe par la décarbonatation du calcaire vers 900 °C dans le four de la cimenterie (CaCO3→CaO + CO2). Sa fabrication induit donc une émission de CO2de nature chimique à laquelle s’ajoute le dégagement de CO2lié à la combustion nécessaire à la chauffe.
9La carbonatation repose sur la transformation des hydrates du ciment en carbonate de calcium CaCO3(calcaire) sous l’action chimique du CO2de l’atmosphère.
10 L’Ifsttar a travaillé sur les aspects positifs de la carbonatation dans le cadre d’un financement par l’Agence nationale de la recherche : projet Crac ou Carbonation of Recycled Aggregates of Concrete, récompensé par le prix du Trophée Eugène Freyssinet en 2011, qui s’est clôturé en 2013.
A retrouver aussi dans Béton[s]le Magazine n° 86.